In the industrial world, valves are critical components that control the flow of fluids, gases, or steam within pipelines and machinery. Among the various types of valves available, electric high-temperature ball valves are particularly indispensable in applications where extreme temperatures need to be managed with precision and efficiency. These valves, powered by electric actuators, offer excellent performance in high-temperature environments, making them crucial for industries such as oil and gas, petrochemicals, power generation, and many others.
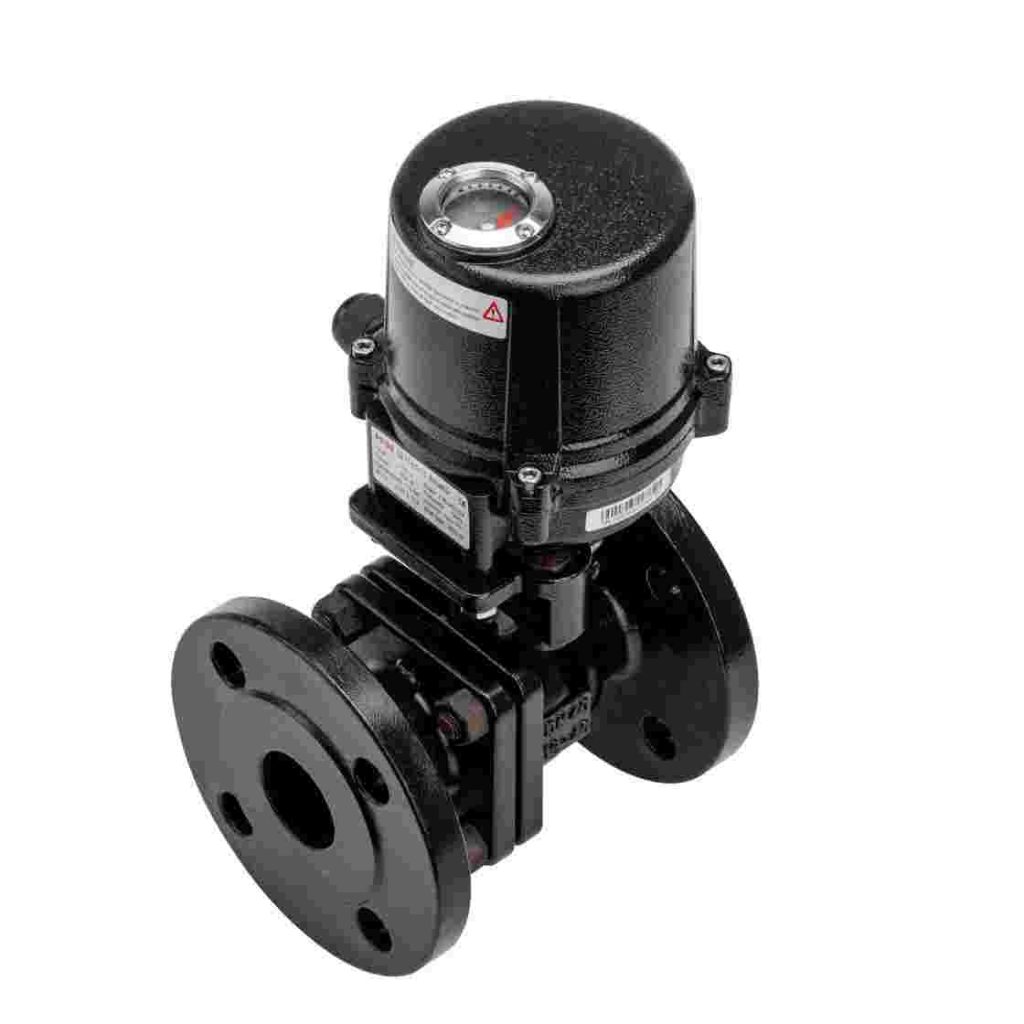
An electric high-temperature ball valve manufacturer plays a pivotal role in ensuring that these essential components are designed, produced, and maintained to meet stringent industry standards. In this article, we will delve into the importance of electric high-temperature ball valves, the key considerations for manufacturers, and the advancements that have made these valves a cornerstone in modern industrial applications.
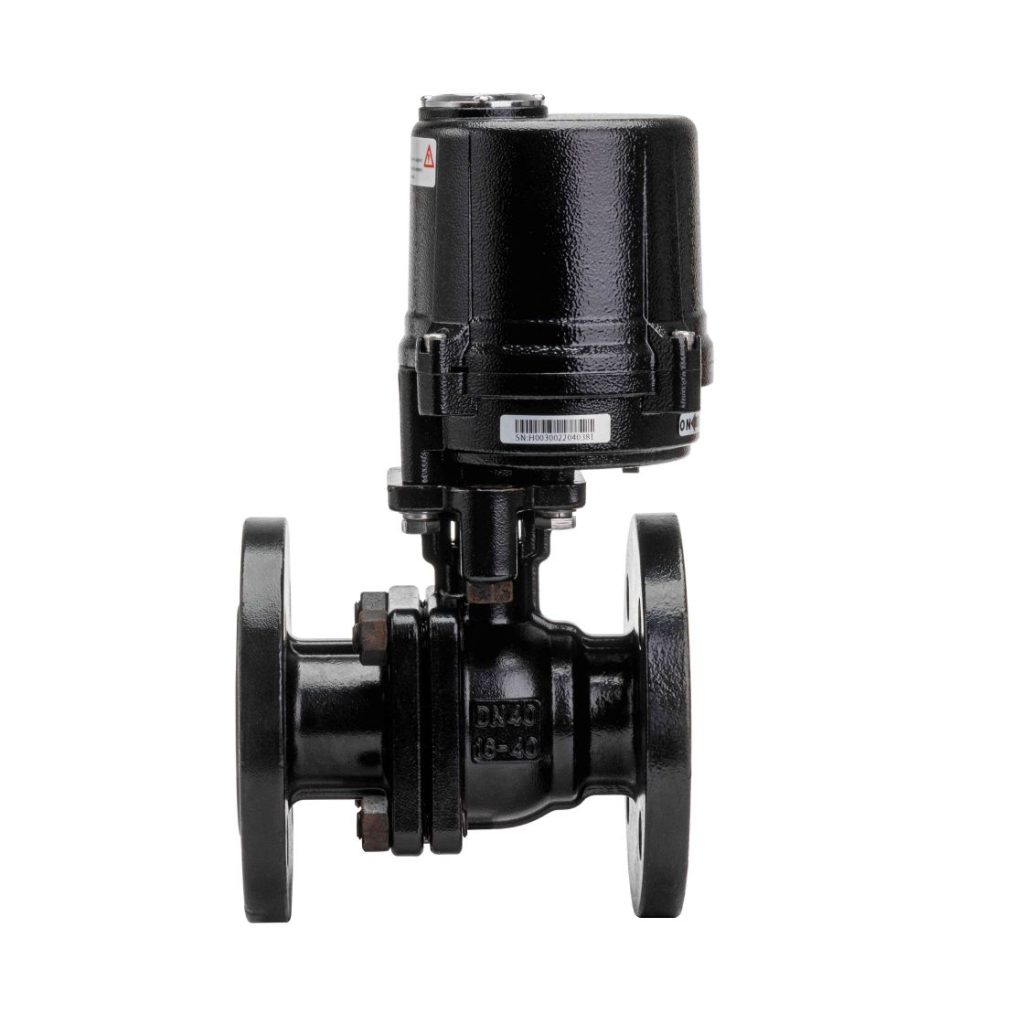
What Are Electric High Temperature Ball Valves? Electric high-temperature ball valves are designed to regulate the flow of liquids, gases, or steam in high-temperature environments, typically above 200°C (392°F). They are called “ball valves” because the internal mechanism consists of a ball with a hole in the center that rotates to control the flow. When the valve is open, the ball is aligned with the pipe, allowing flow; when it is closed, the ball rotates to block the pipe, preventing flow. What sets electric high-temperature ball valves apart from conventional ones is the use of an electric actuator to control the valve’s position. Unlike manual valves that require operators to turn a handle or gear, electric actuators enable automated control of the valve, making it easier to regulate and monitor fluid or gas flow remotely. This is particularly valuable in high-temperature systems where manual operation could pose a risk to safety and efficiency.
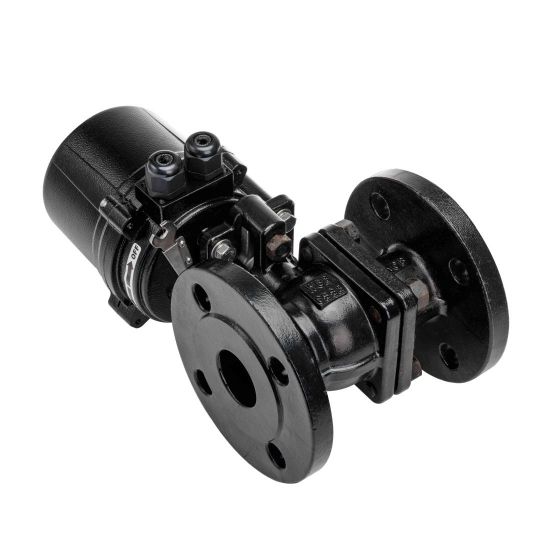
Leave a Reply