In recent years, China has emerged as a leader in the manufacturing of various industrial components, including electric flanged hard seal butterfly valves. These valves play a crucial role in fluid control systems across numerous industries such as water treatment, oil and gas, chemical processing, and power generation. This article delves into the features, applications, and advantages of electric flanged hard seal butterfly valves, highlighting the innovation and expertise of Chinese manufacturers.
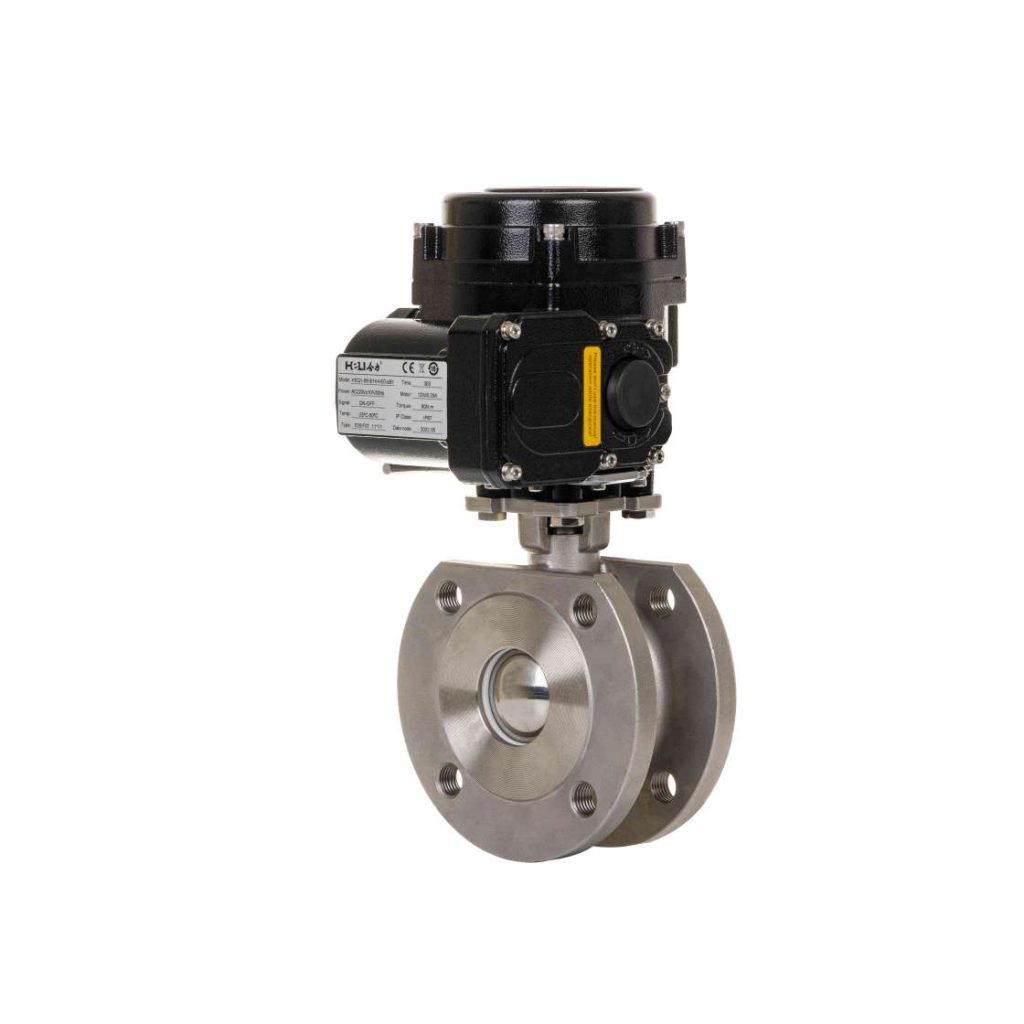
Electric flanged hard seal butterfly valves are designed to offer a reliable solution for isolating and regulating the flow of liquids and gases. The hard seal feature is particularly beneficial as it provides enhanced durability and a leak-tight seal, making it suitable for high-pressure applications. The valve’s construction typically includes a disc that rotates around a central shaft, allowing for easy opening and closing. When the valve is fully open, the disc is positioned parallel to the flow direction, minimizing pressure loss and turbulence.
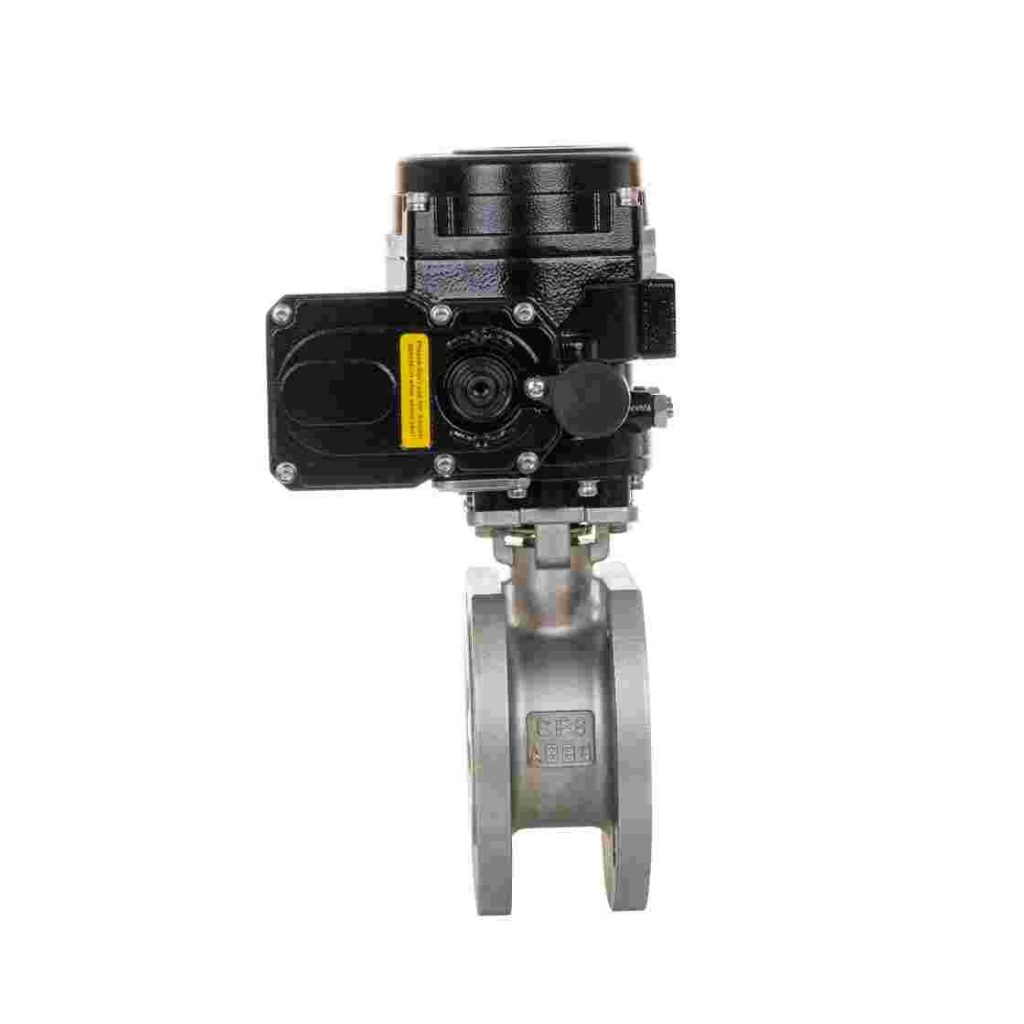
One of the key advantages of electric flanged hard seal butterfly valves is their automation capability. Equipped with electric actuators, these valves can be operated remotely, enhancing operational efficiency and safety. This feature is particularly valuable in large-scale industrial settings where manual operation may pose risks or be impractical. The electric actuators provide precise control over valve positions, allowing for fine adjustments in flow regulation, which is critical for maintaining optimal process conditions. Chinese manufacturers of electric flanged hard seal butterfly valves are renowned for their commitment to quality and innovation. Many of these companies utilize advanced manufacturing techniques and rigorous quality control measures to ensure that their products meet international standards. The integration of cutting-edge technology, such as computer-aided design (CAD) and simulation software, enables manufacturers to optimize valve performance and reliability.
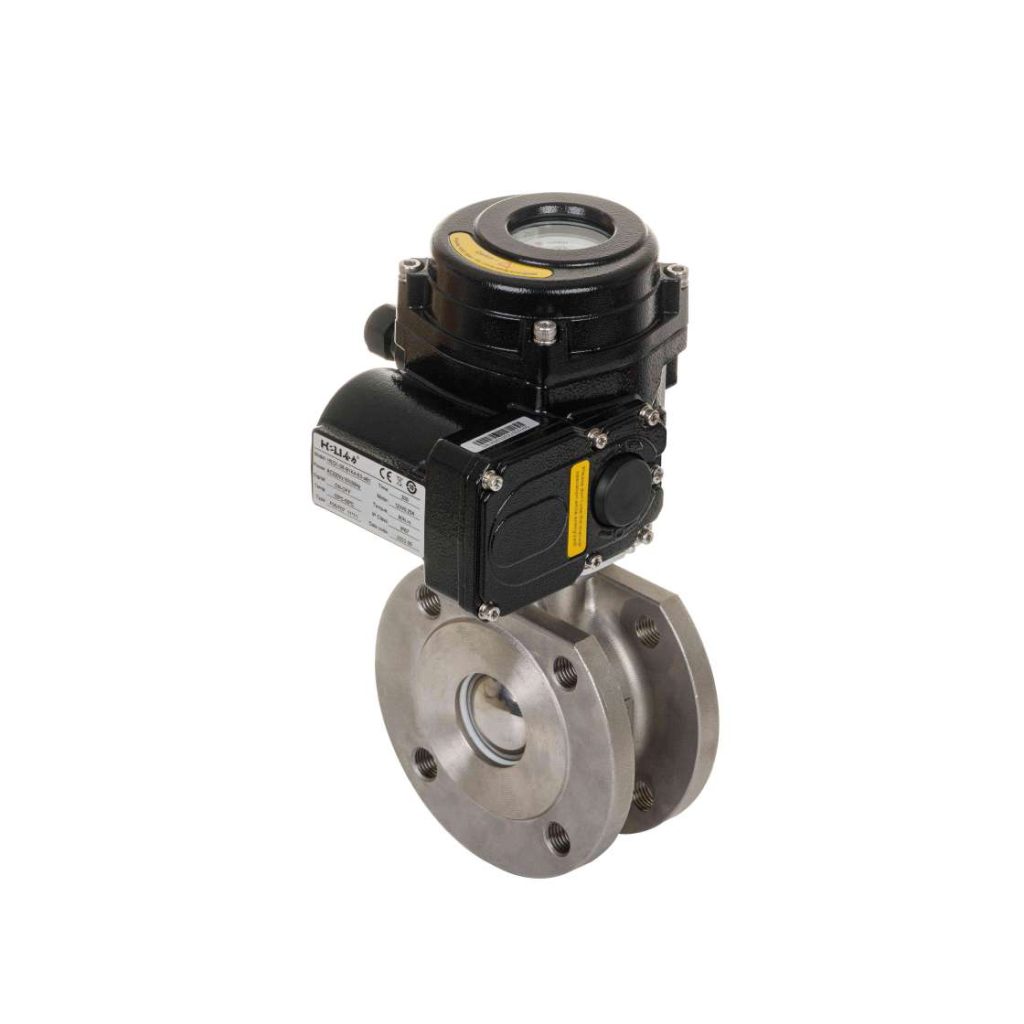
Leave a Reply