Pneumatic actuators are essential components in a wide range of industries, including manufacturing, robotics, automotive, and process control systems. These devices, which convert compressed air into mechanical motion, are fundamental for driving automation processes, enabling precise, reliable, and energy-efficient operations. This article will explore the working principles of pneumatic actuators, their types, applications, and the benefits they offer in various industrial settings.
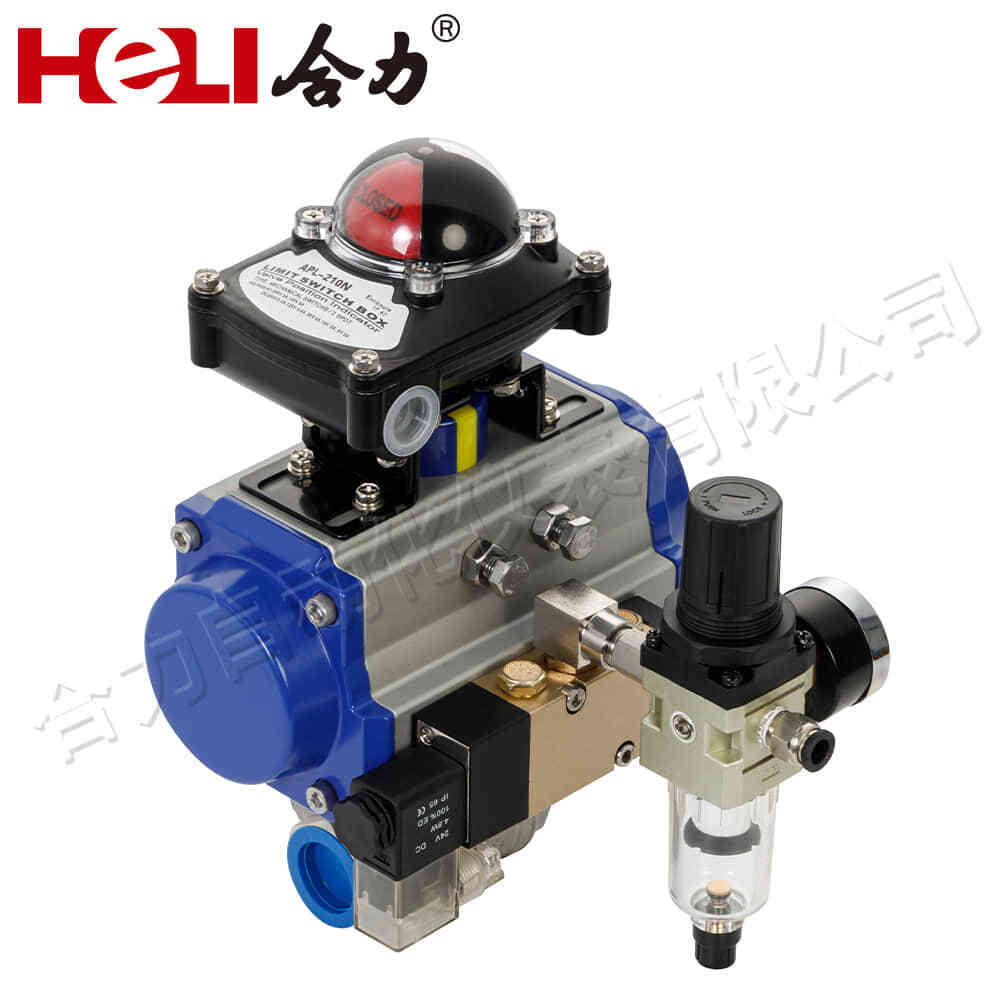
Working Principles of Pneumatic Actuators
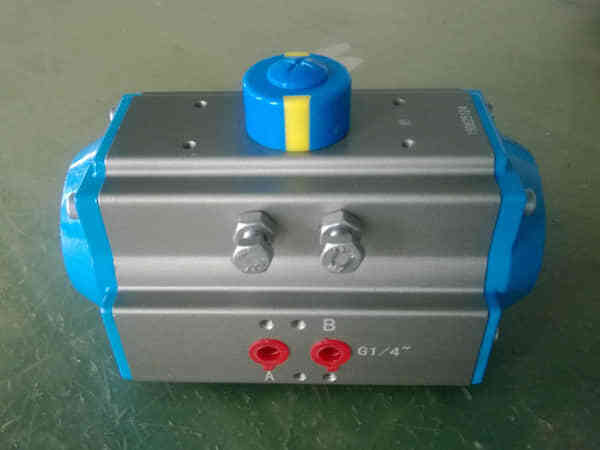
At the heart of a pneumatic actuator is the conversion of compressed air into linear or rotary motion. The system typically consists of an air compressor, valves, tubing, and the actuator itself. Compressed air is fed into the actuator’s chamber, causing a diaphragm or piston to move. This motion is then translated into mechanical work. Pneumatic actuators can generate substantial force with relatively simple and cost-effective equipment, making them ideal for tasks requiring moderate power but high-speed operations. The process begins when compressed air enters the actuator’s cylinder through an inlet valve. The pressure from the air pushes against a piston or diaphragm inside the actuator, moving it to one side. Depending on the actuator’s design, the motion may be linear (back and forth) or rotary (circular). The movement is then transmitted to the mechanical system or machine it controls, such as opening or closing a valve, lifting a component, or driving a piece of equipment.
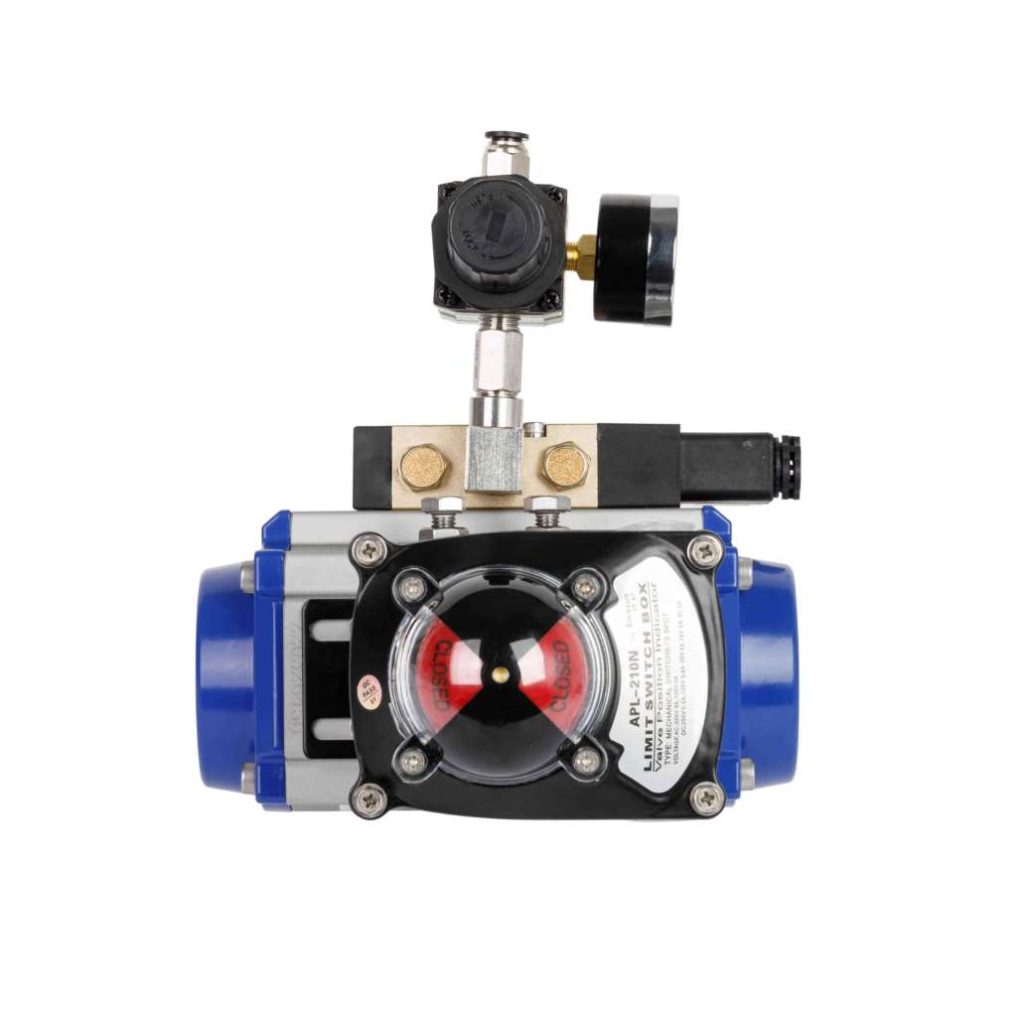
Leave a Reply