Pneumatic actuators are crucial components in many industrial systems, harnessing the power of compressed air to produce mechanical motion. These devices convert the energy stored in compressed air into linear or rotary motion, making them indispensable in various applications ranging from simple control systems to complex manufacturing processes.
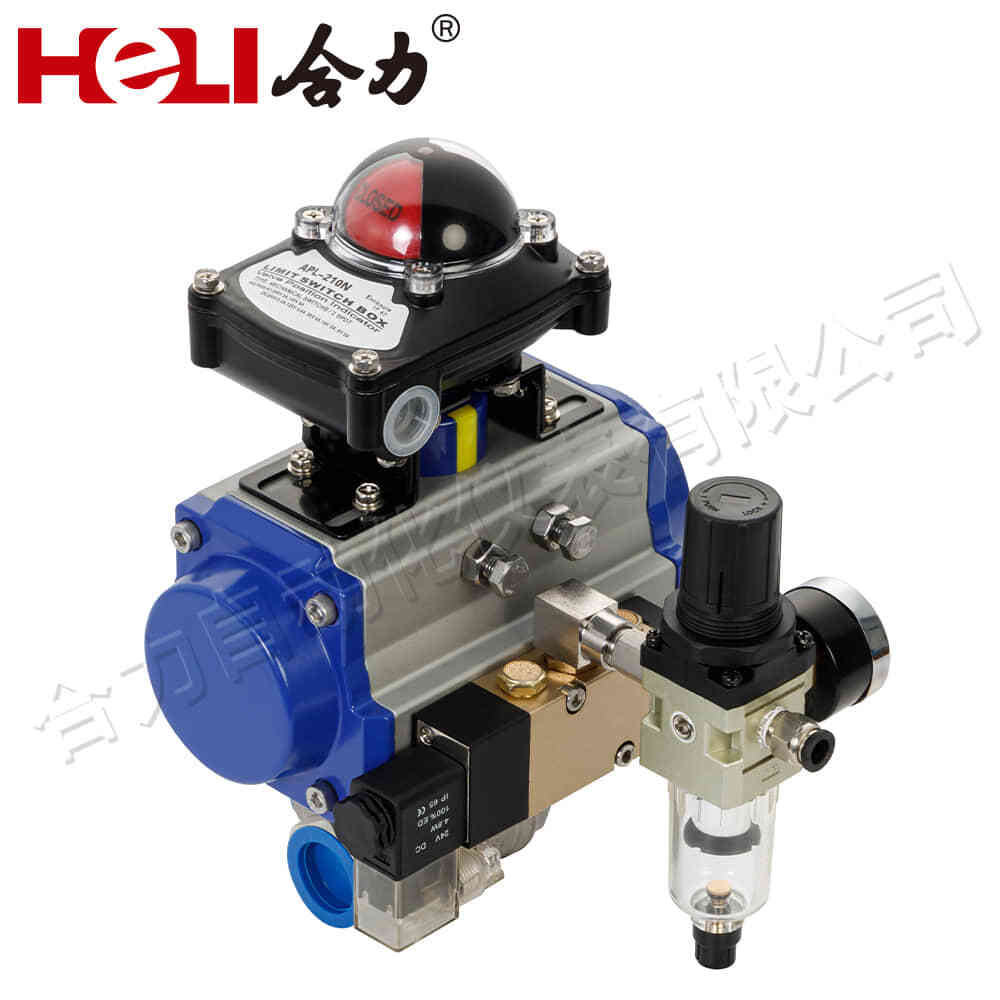
At their core, pneumatic actuators operate on the principle of air pressure. When compressed air is directed into the actuator, it creates a force that moves a piston or a diaphragm. This motion can then be used to perform a wide array of tasks. The simplicity of pneumatic actuators often translates to cost-effectiveness and reliability, which are significant advantages in both high-volume production and critical applications.
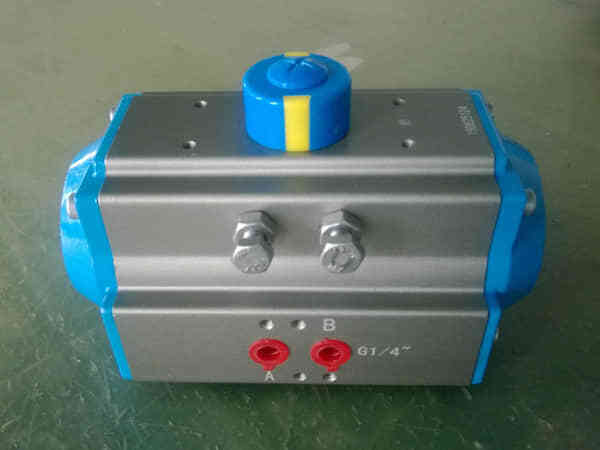
One of the most common types of pneumatic actuators is the double-acting cylinder. In this design, air pressure is used to extend and retract the piston, providing control over the stroke length. This type of actuator is favored for its versatility and the ability to offer precise control over movement. Another prevalent type is the single-acting cylinder, which relies on a spring to return the piston to its original position after the air pressure is released. Single-acting cylinders are typically used in applications where return strokes are less critical or where space is a constraint.
Pneumatic actuators are also categorized by their motion output. Linear actuators produce straight-line motion, while rotary actuators convert air pressure into rotational movement. Rotary actuators are essential in applications where parts need to be turned or positioned at specific angles. For instance, they are widely used in robotics, automated assembly lines, and valve control systems.
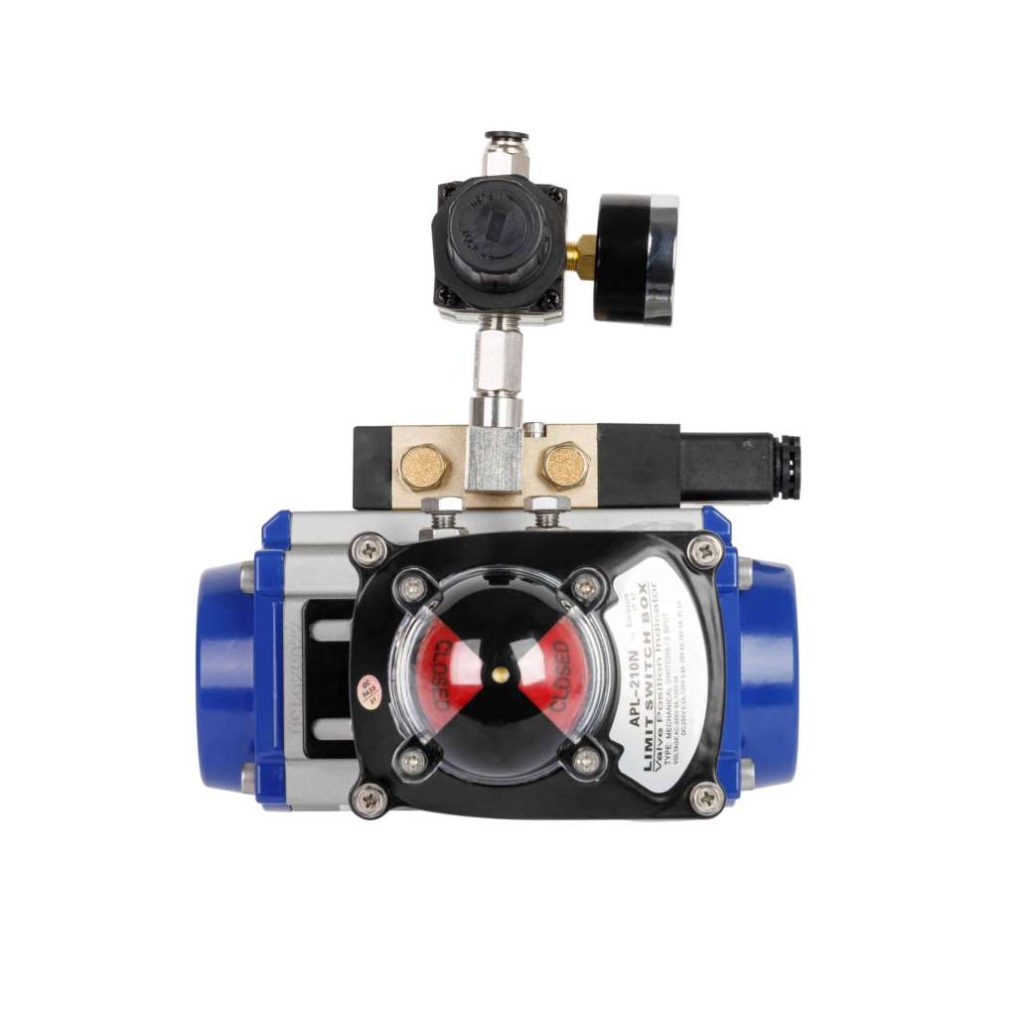
Leave a Reply